A Comprehensive Overview to the Refine and Advantages of Plastic Extrusion
In the vast world of manufacturing, plastic extrusion arises as a extremely efficient and crucial process. Altering raw plastic into continual accounts, it caters to a myriad of industries with its impressive flexibility.
Recognizing the Basics of Plastic Extrusion
While it might show up complex in the beginning glance, the procedure of plastic extrusion is fundamentally basic - plastic extrusion. It is a high-volume production method in which raw plastic is thawed and formed right into a continuous profile. The process begins with the feeding of plastic material, in the form of granules, pellets, or powders, into a heated barrel. The plastic is then thawed using a combination of heat and shear, applied by a revolving screw. As soon as the molten plastic gets to the end of the barrel, it is required with a little opening referred to as a die, shaping it into a preferred type. The shaped plastic is after that cooled down, solidified, and cut into desired lengths, finishing the procedure.
The Technical Refine of Plastic Extrusion Explained
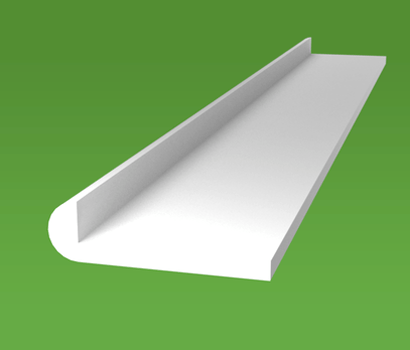
Sorts Of Plastic Suitable for Extrusion
The choice of the right sort of plastic is a crucial aspect of the extrusion procedure. Numerous plastics use distinct residential properties, making them more suited to certain applications. Polyethylene, for instance, is frequently used as a result of its inexpensive and very easy formability. It offers outstanding resistance to chemicals and wetness, making it excellent for items like tubes and containers. Polypropylene is one more popular option due to its high melting point and resistance to tiredness. For even more durable applications, polystyrene and PVC (polyvinyl chloride) are usually chosen for their stamina and longevity. These are common options, the choice ultimately depends on the particular demands of the item being generated. So, understanding these plastic types can substantially boost the extrusion procedure.
Comparing Plastic Extrusion to Various Other Plastic Forming Methods
Recognizing the types of plastic suitable for extrusion leads the way for a more comprehensive conversation on how plastic extrusion piles up against various other plastic forming approaches. These include shot molding, blow molding, and thermoforming. Each approach has its distinct usages and advantages. Shot molding, for instance, is superb for developing elaborate parts, while impact molding is ideal for hollow objects like containers. Thermoforming excels at developing superficial or large components. Plastic extrusion is exceptional when it comes to creating continuous profiles, such as pipelines, seals, and gaskets. It also permits a consistent cross-section along the size of the product. Thus, the choice of method greatly relies Discover More on the end-product requirements and specifications.
Secret Benefits of Plastic Extrusion in Manufacturing
In the realm of production, plastic extrusion offers numerous substantial advantages. One notable advantage is the cost-effectiveness of the process, which makes it an economically enticing production approach. Additionally, this strategy supplies superior product adaptability and enhanced manufacturing rate, consequently enhancing total production effectiveness.
Affordable Manufacturing Approach
Plastic extrusion jumps to the center as an economical production method in manufacturing. In addition, plastic extrusion needs much less energy than standard production methods, contributing to reduced functional costs. In general, the monetary benefits make plastic extrusion a very eye-catching alternative in the production industry.
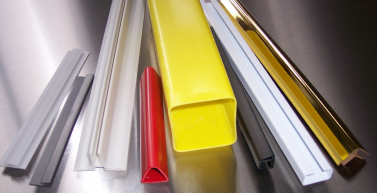
Superior Item Adaptability
Past the cost-effectiveness of plastic extrusion, an additional considerable advantage in manufacturing depend on its remarkable item versatility. This procedure enables the creation of a wide selection of products with differing forms, sizes, and layouts, from straightforward plastic sheets to intricate accounts. The versatility is attributed to the extrusion pass away, which can be personalized to yield the wanted product design. This makes plastic extrusion a perfect service for sectors that need customized plastic parts, such as auto, building, and packaging. The capacity to generate varied products is not just useful in conference details market demands yet likewise in enabling suppliers to check out brand-new product with minimal resources investment. Fundamentally, plastic extrusion's product adaptability promotes technology while improving functional effectiveness.
Enhanced Production Speed
A significant advantage of plastic look these up extrusion exists in its improved informative post production speed. Couple of various other manufacturing procedures can match the rate of plastic extrusion. Furthermore, the capability to preserve consistent high-speed manufacturing without sacrificing product high quality establishes plastic extrusion apart from other techniques.
Real-world Applications and Influences of Plastic Extrusion
In the world of manufacturing, the technique of plastic extrusion holds extensive relevance. The financial benefit of plastic extrusion, primarily its high-volume and cost-effective output, has actually changed manufacturing. The market is persistently striving for technologies in naturally degradable and recyclable materials, suggesting a future where the advantages of plastic extrusion can be preserved without compromising ecological sustainability.
Conclusion
To conclude, plastic extrusion is a reliable and very efficient method of transforming basic materials right into diverse products. It supplies various benefits over other plastic creating methods, consisting of cost-effectiveness, high outcome, minimal waste, and design versatility. Its effect is exceptionally felt in numerous sectors such as building and construction, auto, and customer goods, making it a critical process in today's production landscape.
Diving much deeper right into the technological process of plastic extrusion, it begins with the option of the ideal plastic material. As soon as cooled down, the plastic is reduced right into the required sizes or wound onto reels if the item is a plastic film or sheet - plastic extrusion. Contrasting Plastic Extrusion to Other Plastic Forming Techniques
Comprehending the types of plastic suitable for extrusion leads the method for a wider discussion on exactly how plastic extrusion stacks up against various other plastic creating techniques. Couple of other production procedures can match the speed of plastic extrusion.